At Vectur Energy
we understand that safety is paramount in high-risk industrial environments. A major utility provider recently faced a critical challenge: their outdated gas detection and monitoring system was no longer fit for purpose. In a facility where hazardous gases are a daily reality, ensuring reliable monitoring is not just a regulatory requirement—it’s a necessity for worker safety and operational efficiency.
The Challenge: Outdated Gas Detection Systems
The plant in question, a large industrial wastewater recycling facility, had been relying on an aging gas detection system that was riddled with faults. Over time, the system became unreliable, failing to provide adequate coverage and lacking real-time monitoring capabilities. This posed significant risks, including:
- Unreliable Detection: Faulty equipment left critical areas unmonitored, increasing the likelihood of undetected gas leaks.
- Lack of Integration: The old system did not interface with the plant’s broader control systems, making it difficult for operators to respond promptly to safety alerts.
- Compliance Risks: With stricter health and safety regulations, the plant faced potential non-compliance, endangering both personnel and operations.
Recognising these risks, the utility provider sought a modern solution that would enhance monitoring, improve response times, and ensure regulatory compliance.
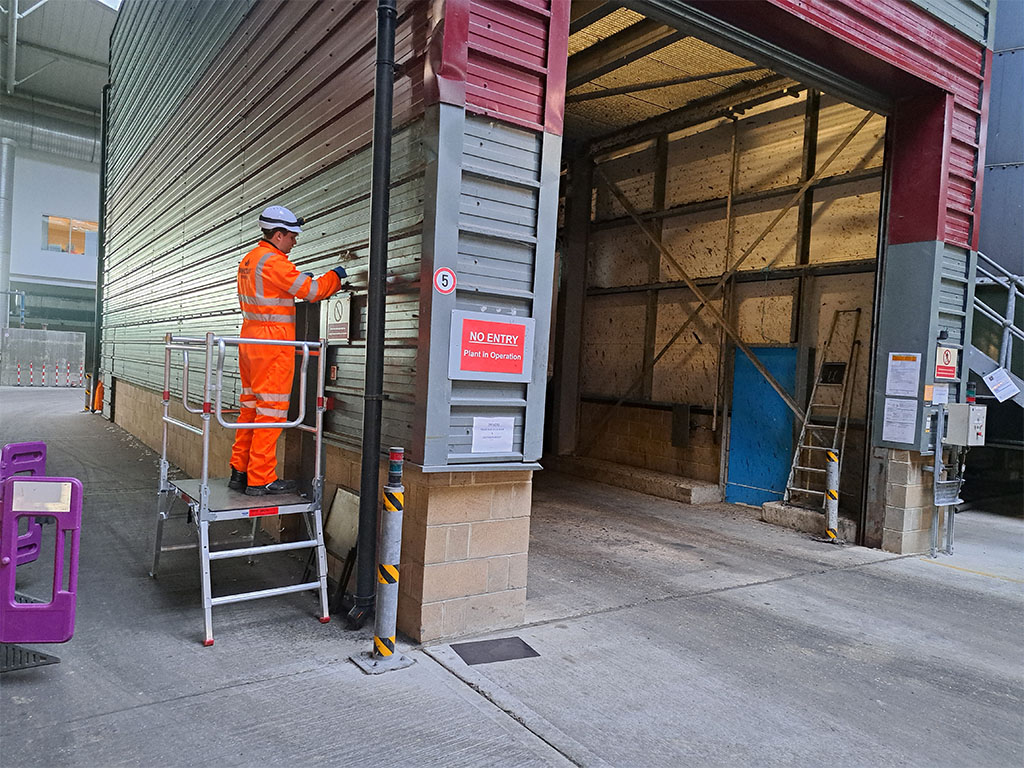
The Solution: A State-of-the-Art Gas Detection System
To address these challenges, Vectur Energy partnered with the client to develop and implement a fully integrated gas detection and monitoring system. The project aimed to:
- Enhance Safety: Provide real-time monitoring of hazardous gases such as hydrogen sulphide, methane, carbon monoxide, and nitrogen dioxide.
- Improve System Integration: Connect seamlessly with the plant’s SCADA (Supervisory Control and Data Acquisition) system to enable automated alerts and shutdown protocols.
- Ensure Compliance: Meet stringent industry safety standards.
With a clear strategy in place, the first phase of the project focused on assessing the existing infrastructure. By testing the electrical integrity of existing cabling, the team identified opportunities to reuse functional components, reducing costs and installation time. This strategic approach laid the groundwork for an efficient and cost-effective upgrade.
Why This Matters
Gas detection systems are the first line of defence against hazardous leaks in industrial settings. Without a reliable system in place, workers face increased risks of exposure, operational downtime, and regulatory penalties. Investing in modern gas detection technology ensures not only compliance but also a safer and more efficient working environment.
In the next update, we’ll dive into how the Vectur Energy team implemented a cutting-edge gas detection system tailored to the plant’s unique requirements. Stay tuned for part two of our project update series: Overcoming Challenges – Designing the Optimal Solution.
For more insights on industrial safety and monitoring solutions, visit our website or get in touch with our team today.
At Vectur Energy
we understand that safety is paramount in high-risk industrial environments. A major utility provider recently faced a critical challenge: their outdated gas detection and monitoring system was no longer fit for purpose. In a facility where hazardous gases are a daily reality, ensuring reliable monitoring is not just a regulatory requirement—it’s a necessity for worker safety and operational efficiency.
The Challenge: Outdated Gas Detection Systems
The plant in question, a large industrial wastewater recycling facility, had been relying on an aging gas detection system that was riddled with faults. Over time, the system became unreliable, failing to provide adequate coverage and lacking real-time monitoring capabilities. This posed significant risks, including:
- Unreliable Detection: Faulty equipment left critical areas unmonitored, increasing the likelihood of undetected gas leaks.
- Lack of Integration: The old system did not interface with the plant’s broader control systems, making it difficult for operators to respond promptly to safety alerts.
- Compliance Risks: With stricter health and safety regulations, the plant faced potential non-compliance, endangering both personnel and operations.
Recognising these risks, the utility provider sought a modern solution that would enhance monitoring, improve response times, and ensure regulatory compliance.
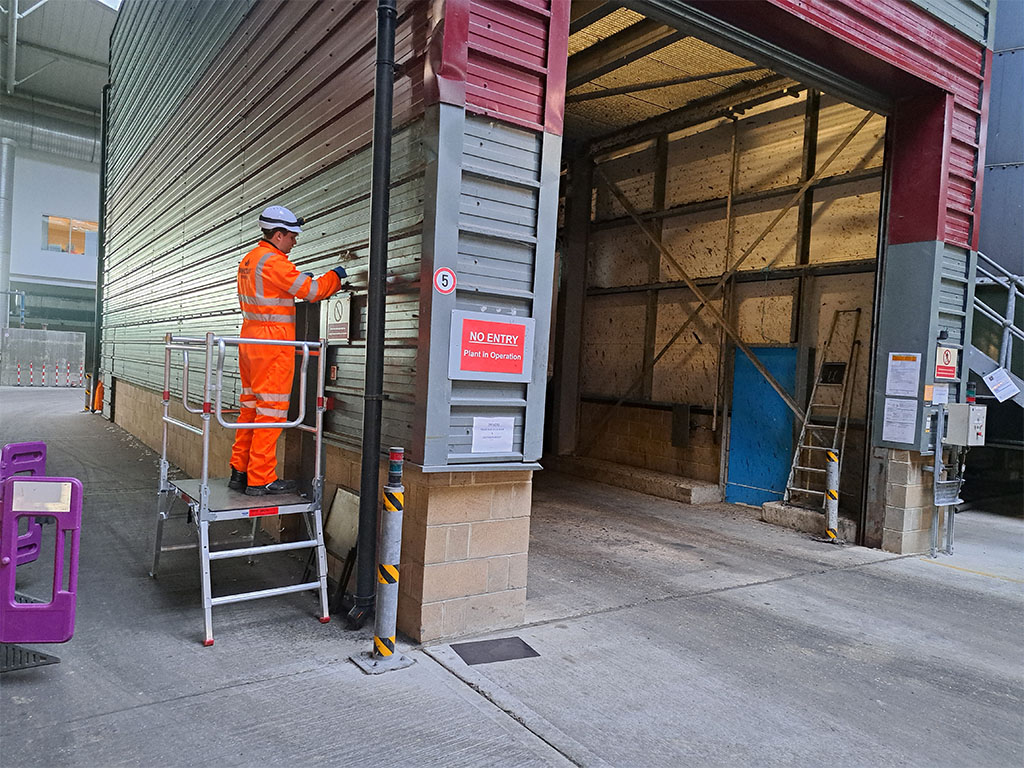
The Solution: A State-of-the-Art Gas Detection System
To address these challenges, Vectur Energy partnered with the client to develop and implement a fully integrated gas detection and monitoring system. The project aimed to:
- Enhance Safety: Provide real-time monitoring of hazardous gases such as hydrogen sulphide, methane, carbon monoxide, and nitrogen dioxide.
- Improve System Integration: Connect seamlessly with the plant’s SCADA (Supervisory Control and Data Acquisition) system to enable automated alerts and shutdown protocols.
- Ensure Compliance: Meet stringent industry safety standards.
With a clear strategy in place, the first phase of the project focused on assessing the existing infrastructure. By testing the electrical integrity of existing cabling, the team identified opportunities to reuse functional components, reducing costs and installation time. This strategic approach laid the groundwork for an efficient and cost-effective upgrade.
Why This Matters
Gas detection systems are the first line of defence against hazardous leaks in industrial settings. Without a reliable system in place, workers face increased risks of exposure, operational downtime, and regulatory penalties. Investing in modern gas detection technology ensures not only compliance but also a safer and more efficient working environment.
In the next update, we’ll dive into how the Vectur Energy team implemented a cutting-edge gas detection system tailored to the plant’s unique requirements. Stay tuned for part two of our project update series: Overcoming Challenges – Designing the Optimal Solution.
For more insights on industrial safety and monitoring solutions, visit our website or get in touch with our team today.