With the challenges identified and a robust design in place,
the next phase of our project at the industrial wastewater recycling plant was implementation and testing. At Vectur Energy, we pride ourselves on executing seamless installations that not only meet industry standards but also enhance safety, efficiency, and long-term reliability.
Implementation Process: A Step-by-Step Approach
Our installation strategy was designed to ensure minimal disruption to plant operations while maintaining the highest level of safety. The process was divided into four key phases:
- Site Survey and Preparation
Before installation, our team conducted a comprehensive site survey to:
- Assess existing infrastructure and ensure compatibility with the new system.
- Identify optimal sensor placement for maximum coverage and efficiency.
- Plan cabling routes, including overhead and underground pathways, to overcome installation challenges in hazardous zones.
- Installation of Advanced Gas Detection Sensors
Our team installed cutting-edge fixed and portable gas detectors across key areas, ensuring:
- Real-time monitoring of hazardous gases such as hydrogen sulfide, methane, carbon monoxide, and nitrogen dioxide.
- Multi-sensor detection capabilities to enhance accuracy and responsiveness.
- Strategic placement in high-risk zones, including storage tanks, pipelines, and confined spaces.
In addition, fiber-optic cables were used to facilitate seamless communication between detection units and control systems, overcoming vast facility distances and volatile environments.
- Integration with Control Systems
One of the most critical steps was integrating the new gas detection system with the plant’s Supervisory Control and Data Acquisition (SCADA) system. This integration enabled:
- Automated safety responses, including immediate shutdown protocols in case of gas leaks.
- A centralised dashboard providing real-time gas level monitoring for operators.
- Efficient alarm and notification systems with both visual and audible alerts.
By integrating with SCADA, the plant’s safety management was significantly improved, ensuring that all safety events were logged, analysed, and acted upon efficiently.
- Calibration, Testing & Compliance Checks
No installation is complete without rigorous testing to ensure optimal performance. Our team conducted:
- Sensor Calibration: Ensuring each detector met precise sensitivity requirements for accurate gas detection.
- Operational Testing: Simulating hazardous conditions to validate system responsiveness.
- Compliance Verification: Conducting thorough inspections to certify that the installation met all industry regulations and safety standards.
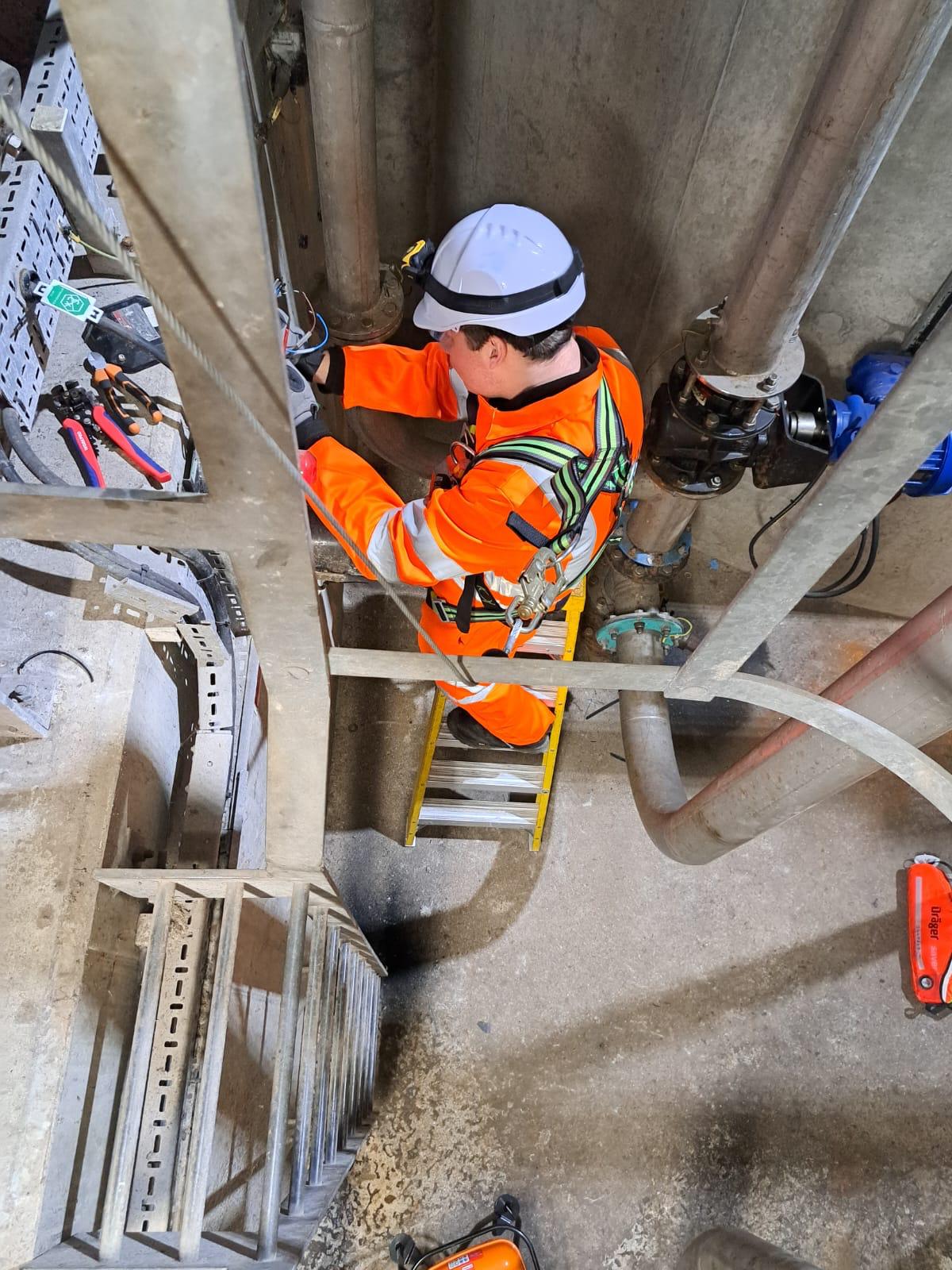
The Impact: A Safer, More Efficient Facility
With the successful implementation and testing of the new gas detection system, the wastewater recycling plant now benefits from:
✅ Real-time gas monitoring, improving hazard detection and response times.
✅ Seamless system integration, ensuring smooth operation with plant-wide safety protocols.
✅ Compliance with industry safety standards, enhancing regulatory confidence.
✅ Minimised risks of gas leaks and exposure, creating a safer working environment for employees.
What’s Next?
With implementation complete, our next update will focus on the long-term benefits and impact of the upgraded gas detection system. Stay tuned for Part 4: Results & Future Impact – A Safer, Smarter Facility, where we highlight cost savings, improved operational efficiency, and peace of mind for our client.
For more information on industrial safety solutions, contact Vectur Energy today.
With the challenges identified and a robust design in place,
the next phase of our project at the industrial wastewater recycling plant was implementation and testing. At Vectur Energy, we pride ourselves on executing seamless installations that not only meet industry standards but also enhance safety, efficiency, and long-term reliability.
Implementation Process: A Step-by-Step Approach
Our installation strategy was designed to ensure minimal disruption to plant operations while maintaining the highest level of safety. The process was divided into four key phases:
- Site Survey and Preparation
Before installation, our team conducted a comprehensive site survey to:
- Assess existing infrastructure and ensure compatibility with the new system.
- Identify optimal sensor placement for maximum coverage and efficiency.
- Plan cabling routes, including overhead and underground pathways, to overcome installation challenges in hazardous zones.
- Installation of Advanced Gas Detection Sensors
Our team installed cutting-edge fixed and portable gas detectors across key areas, ensuring:
- Real-time monitoring of hazardous gases such as hydrogen sulfide, methane, carbon monoxide, and nitrogen dioxide.
- Multi-sensor detection capabilities to enhance accuracy and responsiveness.
- Strategic placement in high-risk zones, including storage tanks, pipelines, and confined spaces.
In addition, fiber-optic cables were used to facilitate seamless communication between detection units and control systems, overcoming vast facility distances and volatile environments.
- Integration with Control Systems
One of the most critical steps was integrating the new gas detection system with the plant’s Supervisory Control and Data Acquisition (SCADA) system. This integration enabled:
- Automated safety responses, including immediate shutdown protocols in case of gas leaks.
- A centralised dashboard providing real-time gas level monitoring for operators.
- Efficient alarm and notification systems with both visual and audible alerts.
By integrating with SCADA, the plant’s safety management was significantly improved, ensuring that all safety events were logged, analysed, and acted upon efficiently.
- Calibration, Testing & Compliance Checks
No installation is complete without rigorous testing to ensure optimal performance. Our team conducted:
- Sensor Calibration: Ensuring each detector met precise sensitivity requirements for accurate gas detection.
- Operational Testing: Simulating hazardous conditions to validate system responsiveness.
- Compliance Verification: Conducting thorough inspections to certify that the installation met all industry regulations and safety standards.
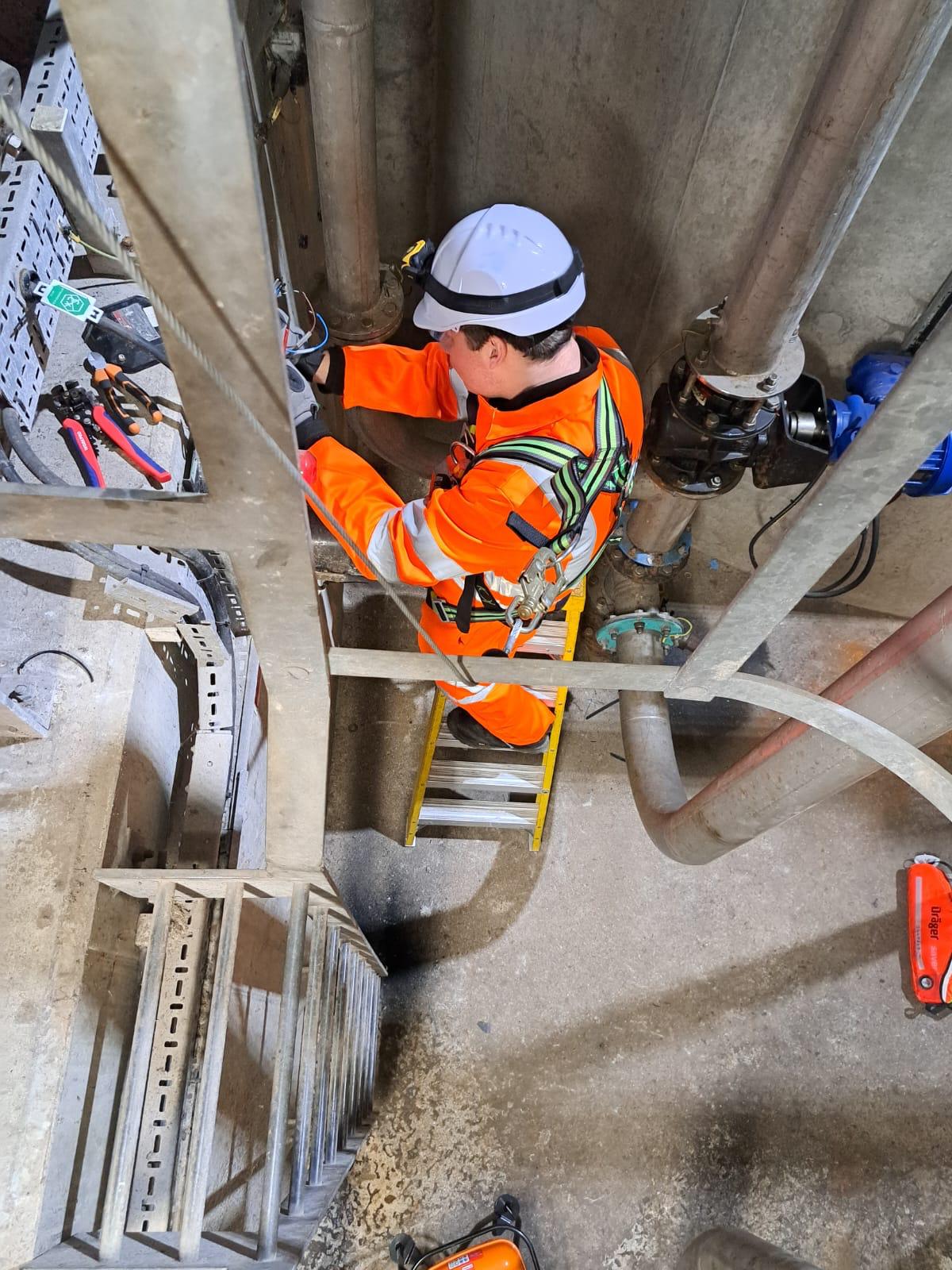
The Impact: A Safer, More Efficient Facility
With the successful implementation and testing of the new gas detection system, the wastewater recycling plant now benefits from:
✅ Real-time gas monitoring, improving hazard detection and response times.
✅ Seamless system integration, ensuring smooth operation with plant-wide safety protocols.
✅ Compliance with industry safety standards, enhancing regulatory confidence.
✅ Minimised risks of gas leaks and exposure, creating a safer working environment for employees.
What’s Next?
With implementation complete, our next update will focus on the long-term benefits and impact of the upgraded gas detection system. Stay tuned for Part 4: Results & Future Impact – A Safer, Smarter Facility, where we highlight cost savings, improved operational efficiency, and peace of mind for our client.
For more information on industrial safety solutions, contact Vectur Energy today.