Following our initial assessment
of the outdated gas detection system at a major industrial wastewater recycling plant, the next step was to design a robust and fully integrated solution. At Vectur Energy, we believe that engineering challenges should be met with strategic innovation, ensuring safety and efficiency without unnecessary disruptions to operations.
Key Challenges in System Design
Before implementation, our team identified several obstacles that required strategic solutions:
- Outdated Equipment: The plant’s existing gas monitoring system had been non-functional for years, with persistent faults and missing essential features such as real-time monitoring and centralised control.
- Limited Coverage Areas: The previous system left key areas unmonitored, creating potential blind spots where hazardous gases could accumulate undetected.
- Integration with Control Systems: The old setup did not effectively interface with the plant’s broader safety and monitoring infrastructure, leading to delays in responding to potential hazards.
- Regulatory Compliance: Meeting industry-specific health and safety standards was a top priority, ensuring the plant maintained compliance with the latest regulations.
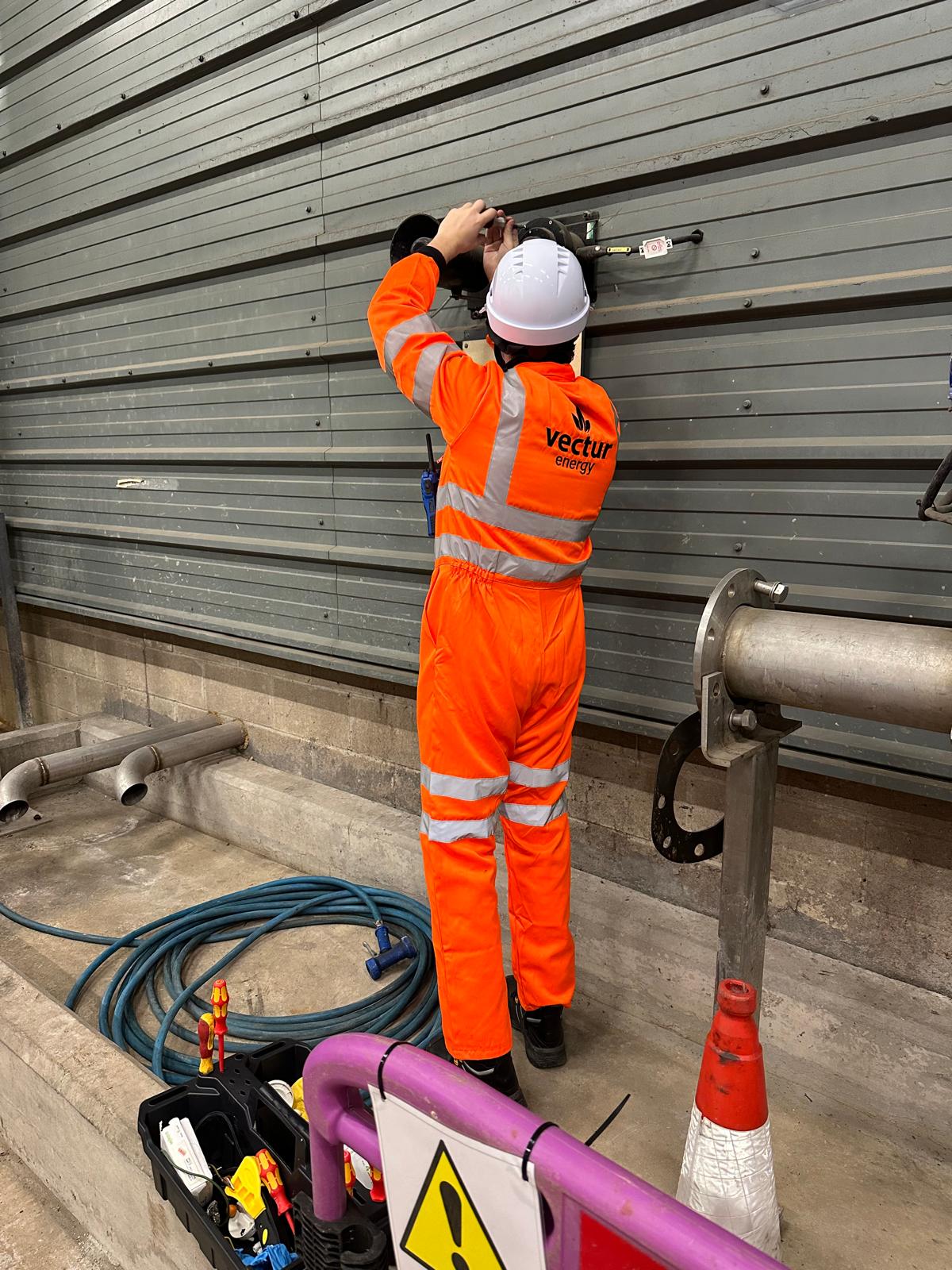
Crafting the Solution: A Modern, Integrated Gas Detection System
To address these challenges, our expert team at Vectur Energy developed a comprehensive plan that prioritised safety, efficiency, and seamless integration.
- Engineering a Reliable Detection Network
Our approach began with extensive testing of the existing cabling infrastructure to assess its integrity. By leveraging functional components from the previous system, we significantly reduced costs and installation time. Our engineers:
- Conducted electrical integrity tests on non-functioning system cables.
- Recycled viable infrastructure components, ensuring cost-effectiveness.
- Designed a new layout for sensor placement to provide complete facility coverage.
- Advanced Sensor Deployment
We installed state-of-the-art fixed and portable gas detectors capable of monitoring hazardous gases such as hydrogen sulfide, methane, carbon monoxide, and nitrogen dioxide. These sensors featured:
- Multi-sensor detection capabilities, allowing real-time monitoring of multiple gas types.
- Strategic placement in high-risk zones, including storage tanks, pipelines, and confined spaces.
- Integration with alarm systems for immediate visual and audio alerts.
- Seamless System Integration
One of the biggest hurdles was ensuring that the new gas detection system seamlessly integrated with the plant’s Supervisory Control and Data Acquisition (SCADA) system. This integration enabled:
- Automated safety responses, including shutdown protocols in case of gas leaks.
- A centralised dashboard providing real-time data and alerts to plant operators.
- Fiber-optic communication between control panels, overcoming installation challenges in hazardous and non-hazardous areas.
Setting the Stage for Implementation
By meticulously planning and overcoming these challenges, we laid the foundation for a successful system installation. Our tailored approach not only enhanced safety but also ensured long-term operational efficiency and compliance.
In our next update, we will delve into the implementation process—covering site survey, installation, and rigorous testing to ensure the system’s optimal performance. Stay tuned for Bringing Safety to Life – Implementation & Testing in our project update series.
For more insights into industrial safety and cutting-edge monitoring solutions, contact Vectur Energy today.
Following our initial assessment
of the outdated gas detection system at a major industrial wastewater recycling plant, the next step was to design a robust and fully integrated solution. At Vectur Energy, we believe that engineering challenges should be met with strategic innovation, ensuring safety and efficiency without unnecessary disruptions to operations.
Key Challenges in System Design
Before implementation, our team identified several obstacles that required strategic solutions:
- Outdated Equipment: The plant’s existing gas monitoring system had been non-functional for years, with persistent faults and missing essential features such as real-time monitoring and centralised control.
- Limited Coverage Areas: The previous system left key areas unmonitored, creating potential blind spots where hazardous gases could accumulate undetected.
- Integration with Control Systems: The old setup did not effectively interface with the plant’s broader safety and monitoring infrastructure, leading to delays in responding to potential hazards.
- Regulatory Compliance: Meeting industry-specific health and safety standards was a top priority, ensuring the plant maintained compliance with the latest regulations.
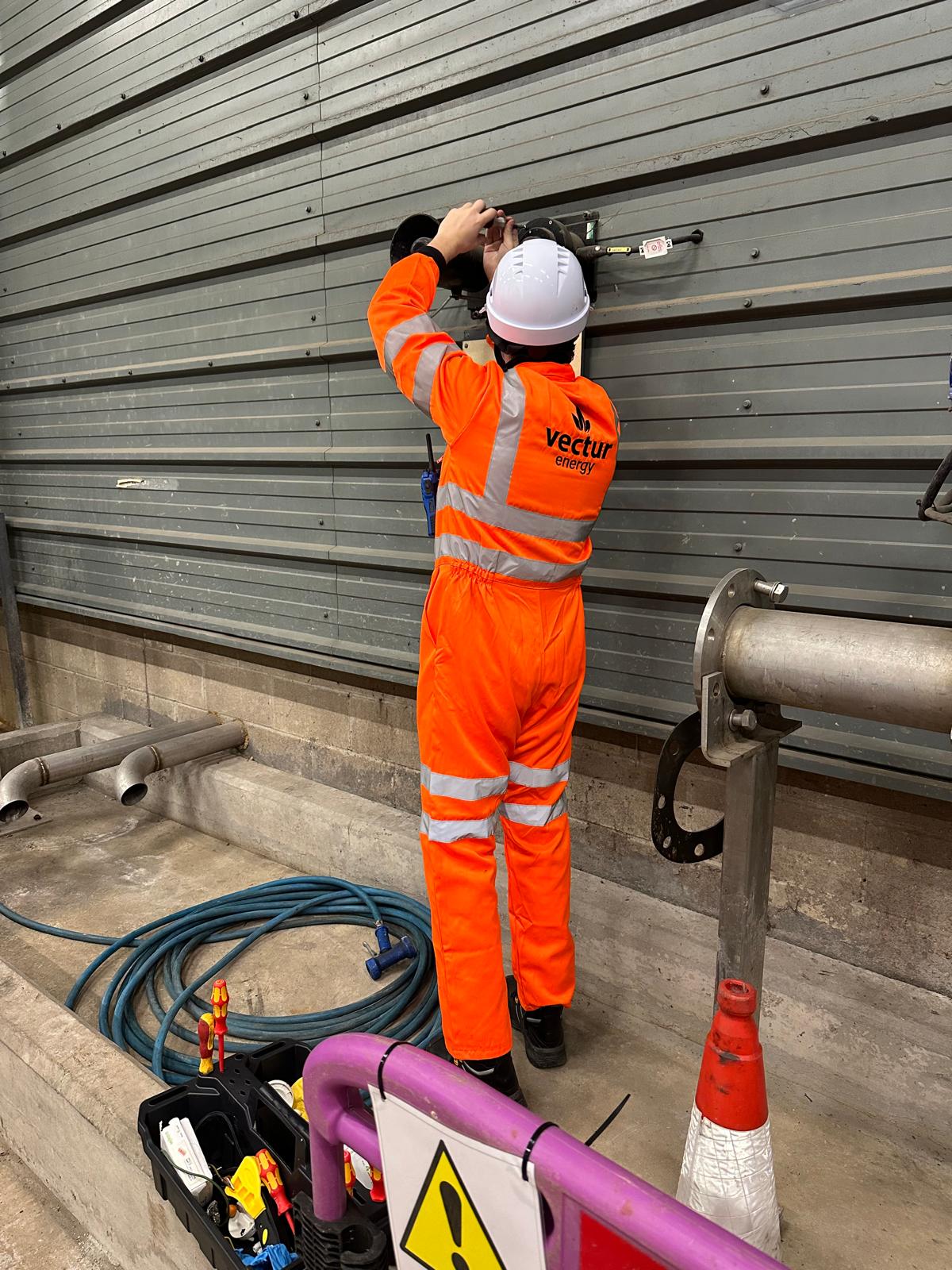
Crafting the Solution: A Modern, Integrated Gas Detection System
To address these challenges, our expert team at Vectur Energy developed a comprehensive plan that prioritised safety, efficiency, and seamless integration.
- Engineering a Reliable Detection Network
Our approach began with extensive testing of the existing cabling infrastructure to assess its integrity. By leveraging functional components from the previous system, we significantly reduced costs and installation time. Our engineers:
- Conducted electrical integrity tests on non-functioning system cables.
- Recycled viable infrastructure components, ensuring cost-effectiveness.
- Designed a new layout for sensor placement to provide complete facility coverage.
- Advanced Sensor Deployment
We installed state-of-the-art fixed and portable gas detectors capable of monitoring hazardous gases such as hydrogen sulfide, methane, carbon monoxide, and nitrogen dioxide. These sensors featured:
- Multi-sensor detection capabilities, allowing real-time monitoring of multiple gas types.
- Strategic placement in high-risk zones, including storage tanks, pipelines, and confined spaces.
- Integration with alarm systems for immediate visual and audio alerts.
- Seamless System Integration
One of the biggest hurdles was ensuring that the new gas detection system seamlessly integrated with the plant’s Supervisory Control and Data Acquisition (SCADA) system. This integration enabled:
- Automated safety responses, including shutdown protocols in case of gas leaks.
- A centralised dashboard providing real-time data and alerts to plant operators.
- Fiber-optic communication between control panels, overcoming installation challenges in hazardous and non-hazardous areas.
Setting the Stage for Implementation
By meticulously planning and overcoming these challenges, we laid the foundation for a successful system installation. Our tailored approach not only enhanced safety but also ensured long-term operational efficiency and compliance.
In our next update, we will delve into the implementation process—covering site survey, installation, and rigorous testing to ensure the system’s optimal performance. Stay tuned for Bringing Safety to Life – Implementation & Testing in our project update series.
For more insights into industrial safety and cutting-edge monitoring solutions, contact Vectur Energy today.