In today’s competitive energy sector
Best Practices for Reliable HV Cable Jointing in Onshore Wind Projects
High Voltage (HV) cable jointing is a critical aspect of onshore wind projects, ensuring that electrical power generated by wind turbines is efficiently transmitted to the grid. Reliable HV cable jointing minimises downtime, enhances the lifespan of the cables, and ensures the overall efficiency and safety of the wind farm. Here, we provide a comprehensive guide on best practices for ensuring reliable and efficient HV cable jointing in onshore wind projects.
Pre-Installation Planning
Detailed Site Assessment
Before beginning any HV cable jointing work, conduct a thorough site assessment. Understand the terrain, soil conditions, and environmental factors that might affect cable installation and jointing.
Cable Route Planning
Plan the cable route meticulously to avoid areas prone to flooding, heavy machinery movement, or other environmental risks. Ensure the route minimises the number of joints required to reduce potential points of failure.
Material Selection
Choose high-quality, durable materials that meet industry standards. Ensure that all materials, including cables, joints, and accessories, are compatible and suited for the specific environmental conditions of the site.
Training and Certification
Skilled Workforce
Ensure that all personnel involved in HV cable jointing are adequately trained and certified. Regular training sessions should be conducted to keep the team updated with the latest techniques and safety protocols.
Specialised Training Programmes
Invest in specialised training programmes for technicians focusing on the unique challenges of onshore wind projects. Certification programmes can provide in-depth knowledge and hands-on experience.
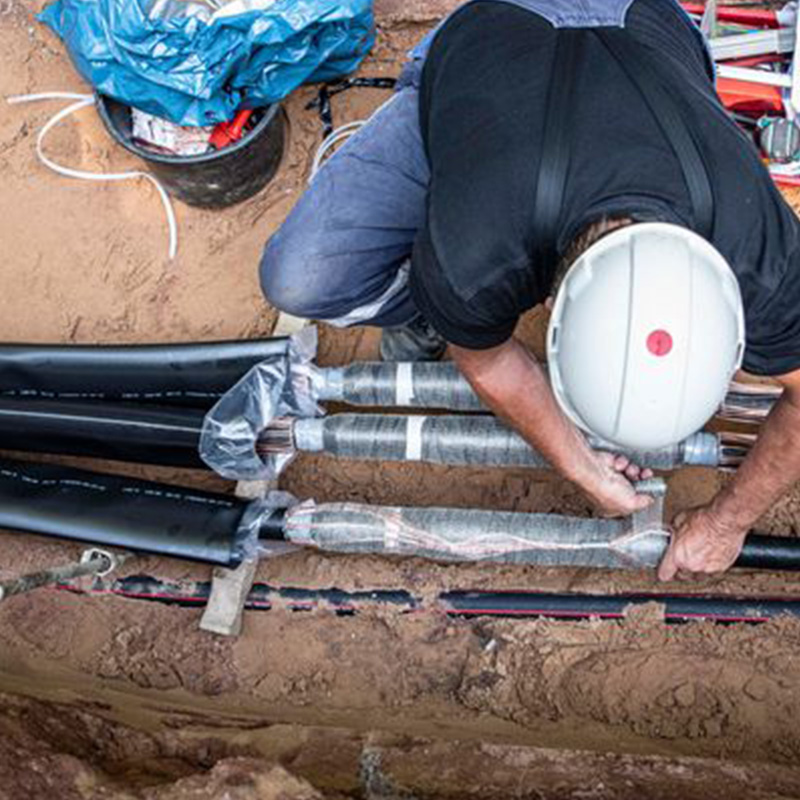
Jointing Techniques and Procedures
Clean and Controlled Environment
Perform cable jointing in a clean and controlled environment to prevent contamination. Use portable shelters or jointing huts if working in open fields to protect the jointing area from dust and moisture.
Proper Cable Preparation
Ensure proper preparation of the cable ends before jointing. This includes precise cutting, stripping, and cleaning of the insulation. Follow manufacturer guidelines meticulously to avoid damaging the cable.
Use of Specialised Tools
Utilise specialised tools designed for HV cable jointing. These tools ensure precision and reduce the risk of damage during installation. Regularly calibrate and maintain tools to ensure optimal performance.
Testing and Quality Assurance
Pre-Jointing Tests
Conduct pre-jointing tests such as insulation resistance and continuity tests to identify any potential issues before jointing begins. This helps in ensuring the cables are in good condition and ready for jointing.
Post-Jointing Tests
After completing the joint, perform post-jointing tests to verify the integrity and performance of the joint. High-voltage testing and partial discharge testing are critical to ensuring the joint can withstand operational stresses.
Documentation and Traceability
Detailed Record Keeping
Maintain detailed records of all jointing activities, including the type of materials used, personnel involved, and test results. This documentation is essential for future maintenance and troubleshooting.
Traceability Systems
Implement traceability systems to track each joint’s history. This can include tagging joints with unique identifiers and recording installation data in a centralised database.
Regular Maintenance and Inspections
Scheduled Inspections
Conduct regular inspections of HV cable joints to detect any signs of wear, degradation, or potential failure. Scheduled maintenance can prevent minor issues from escalating into major problems.
Condition Monitoring
Implement condition monitoring systems that continuously assess the health of HV cable joints. Advanced sensors and monitoring tools can provide real-time data on joint performance, enabling proactive maintenance.
Safety Protocols
Adherence to Safety Standards
Ensure strict adherence to safety standards and regulations throughout the jointing process. This includes wearing appropriate personal protective equipment (PPE) and following safety procedures.
Emergency Preparedness
Prepare for emergencies by having contingency plans in place. Train the team to handle potential hazards such as electrical faults, fires, or equipment failures.
Conclusion
Reliable HV cable jointing is essential for the efficiency and safety of onshore wind projects. By following these best practices—detailed planning, skilled workforce, proper techniques, rigorous testing, thorough documentation, regular maintenance, and strict safety protocols—onshore wind farms can achieve optimal performance and longevity. Investing in high-quality materials, specialised training, and advanced monitoring systems will pay dividends in ensuring the reliability and efficiency of HV cable jointing in the onshore wind sector.
In today’s competitive energy sector
Best Practices for Reliable HV Cable Jointing in Onshore Wind Projects
High Voltage (HV) cable jointing is a critical aspect of onshore wind projects, ensuring that electrical power generated by wind turbines is efficiently transmitted to the grid. Reliable HV cable jointing minimises downtime, enhances the lifespan of the cables, and ensures the overall efficiency and safety of the wind farm. Here, we provide a comprehensive guide on best practices for ensuring reliable and efficient HV cable jointing in onshore wind projects.
Pre-Installation Planning
Detailed Site Assessment
Before beginning any HV cable jointing work, conduct a thorough site assessment. Understand the terrain, soil conditions, and environmental factors that might affect cable installation and jointing.
Cable Route Planning
Plan the cable route meticulously to avoid areas prone to flooding, heavy machinery movement, or other environmental risks. Ensure the route minimises the number of joints required to reduce potential points of failure.
Material Selection
Choose high-quality, durable materials that meet industry standards. Ensure that all materials, including cables, joints, and accessories, are compatible and suited for the specific environmental conditions of the site.
Training and Certification
Skilled Workforce
Ensure that all personnel involved in HV cable jointing are adequately trained and certified. Regular training sessions should be conducted to keep the team updated with the latest techniques and safety protocols.
Specialised Training Programmes
Invest in specialised training programmes for technicians focusing on the unique challenges of onshore wind projects. Certification programmes can provide in-depth knowledge and hands-on experience.
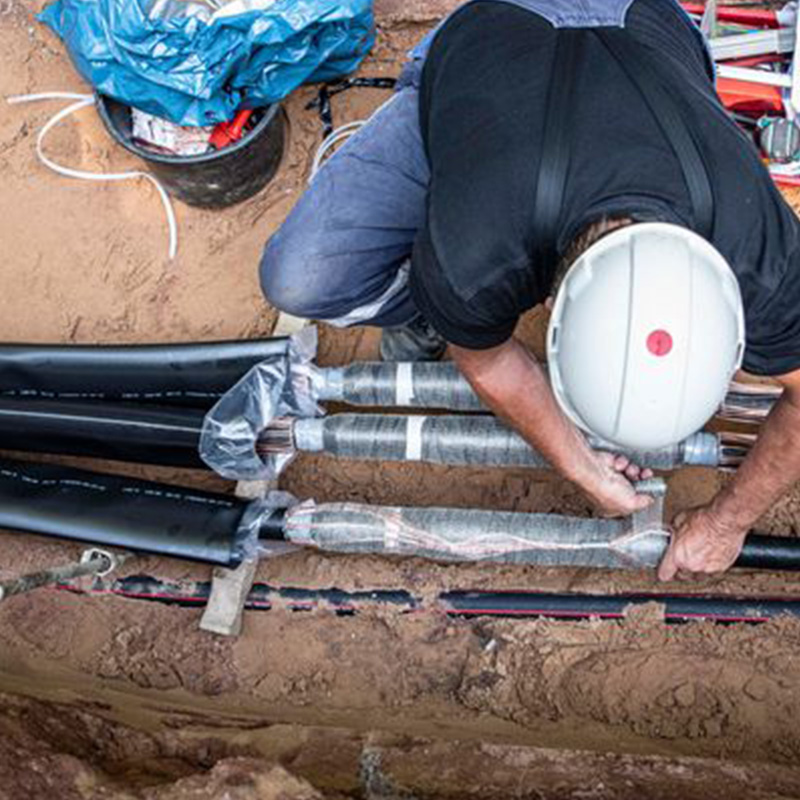
Jointing Techniques and Procedures
Clean and Controlled Environment
Perform cable jointing in a clean and controlled environment to prevent contamination. Use portable shelters or jointing huts if working in open fields to protect the jointing area from dust and moisture.
Proper Cable Preparation
Ensure proper preparation of the cable ends before jointing. This includes precise cutting, stripping, and cleaning of the insulation. Follow manufacturer guidelines meticulously to avoid damaging the cable.
Use of Specialised Tools
Utilise specialised tools designed for HV cable jointing. These tools ensure precision and reduce the risk of damage during installation. Regularly calibrate and maintain tools to ensure optimal performance.
Testing and Quality Assurance
Pre-Jointing Tests
Conduct pre-jointing tests such as insulation resistance and continuity tests to identify any potential issues before jointing begins. This helps in ensuring the cables are in good condition and ready for jointing.
Post-Jointing Tests
After completing the joint, perform post-jointing tests to verify the integrity and performance of the joint. High-voltage testing and partial discharge testing are critical to ensuring the joint can withstand operational stresses.
Documentation and Traceability
Detailed Record Keeping
Maintain detailed records of all jointing activities, including the type of materials used, personnel involved, and test results. This documentation is essential for future maintenance and troubleshooting.
Traceability Systems
Implement traceability systems to track each joint’s history. This can include tagging joints with unique identifiers and recording installation data in a centralised database.
Regular Maintenance and Inspections
Scheduled Inspections
Conduct regular inspections of HV cable joints to detect any signs of wear, degradation, or potential failure. Scheduled maintenance can prevent minor issues from escalating into major problems.
Condition Monitoring
Implement condition monitoring systems that continuously assess the health of HV cable joints. Advanced sensors and monitoring tools can provide real-time data on joint performance, enabling proactive maintenance.
Safety Protocols
Adherence to Safety Standards
Ensure strict adherence to safety standards and regulations throughout the jointing process. This includes wearing appropriate personal protective equipment (PPE) and following safety procedures.
Emergency Preparedness
Prepare for emergencies by having contingency plans in place. Train the team to handle potential hazards such as electrical faults, fires, or equipment failures.
Conclusion
Reliable HV cable jointing is essential for the efficiency and safety of onshore wind projects. By following these best practices—detailed planning, skilled workforce, proper techniques, rigorous testing, thorough documentation, regular maintenance, and strict safety protocols—onshore wind farms can achieve optimal performance and longevity. Investing in high-quality materials, specialised training, and advanced monitoring systems will pay dividends in ensuring the reliability and efficiency of HV cable jointing in the onshore wind sector.