Client Background:
BP, a global energy company, previously enlisted our current directors to operate within the Rumaila oil field in Iraq as part of the Rumaila Operating Organisation (ROO). ROO was a collaboration between SOC, CNOOC, and BP, focused on the redevelopment of the Rumaila oil field. At the inception of our involvement, there was a notable absence of an Integrity department within the wells section, presenting an opportunity to establish and implement a comprehensive Quality Management System (QMS) from the ground up.
Challenges:
The complexity of having three operators involved, along with a diverse multinational staff and service providers, posed significant challenges. The task required the establishment of an integrity department that would closely collaborate with the Drilling, Workover, and Well Service departments, as well as the creation of an audit department spanning the entire wells division.
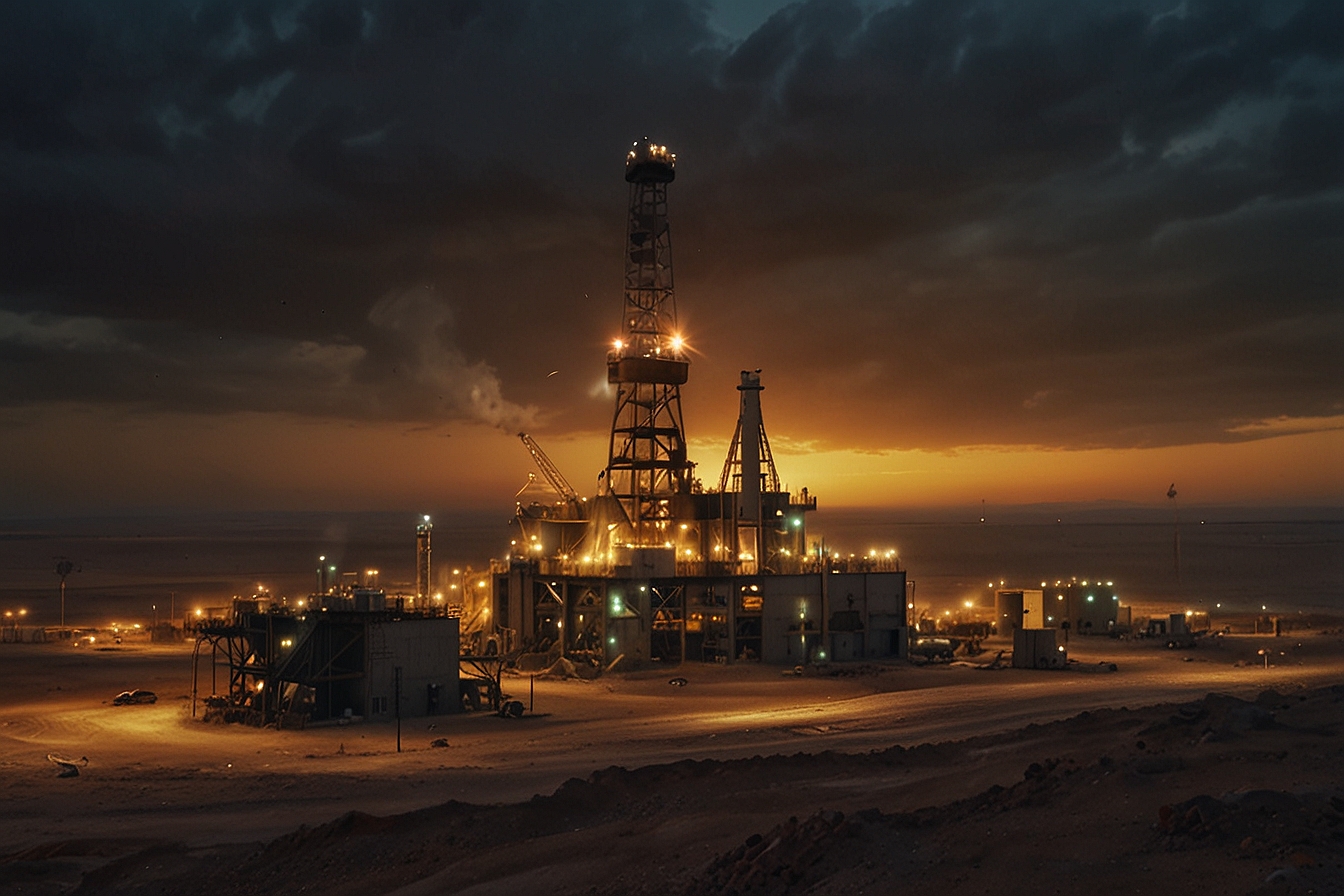
Approach:
Close collaboration with departmental managers was key to building and integrating an efficient, fit-for-purpose QMS that could be uniformly adopted across the wells department. The implementation strategy focused on setting clear expectations for subcontractors, including key performance indicators (KPIs) for both operational delivery and equipment quality. A unique aspect of our approach was the inclusion of subcontractors’ own QMS’s as part of the audit criteria.
Implementation and Results:
The implementation of the QMS resulted in tangible improvements in both the quality and efficiency of services provided by subcontractors, as well as enhanced operational effectiveness within the well team. The emphasis on high-quality documentation and efficient implementation allowed for the Integrity/Audit team to remain lean, with line managers retaining responsibility and control over their respective areas of business.
Key Success Factors:
Collaboration
Close working relationships with departmental managers facilitated the development and integration of the QMS.
Clear Expectations
Setting clear expectations and KPIs for subcontractors ensured accountability and drove performance improvements.
Implementation
High-quality documentation and efficient implementation minimised overhead, allowing for effective control by line managers.
Cultural Sensitivity:
The successful collaboration of a multicultural international team demonstrated the effectiveness of cohesive teamwork in challenging conditions.
Conclusion:
The implementation of a comprehensive QMS in the Rumaila oil field exemplifies how effective collaboration, clear expectations, and efficient implementation can drive significant improvements in safety, efficiency, and quality within a multinational operational environment. This case study serves as a testament to the successful adaptation and implementation of best practices in demanding and diverse work environments.